What is Porosity in Welding: Best Practices for Staying Clear Of Permeable Welds
What is Porosity in Welding: Best Practices for Staying Clear Of Permeable Welds
Blog Article
Porosity in Welding: Identifying Common Issues and Implementing Best Practices for Prevention
Porosity in welding is a prevalent issue that frequently goes unnoticed up until it triggers considerable troubles with the honesty of welds. In this discussion, we will check out the crucial elements adding to porosity formation, analyze its damaging results on weld efficiency, and talk about the best practices that can be taken on to decrease porosity event in welding procedures.
Typical Reasons of Porosity
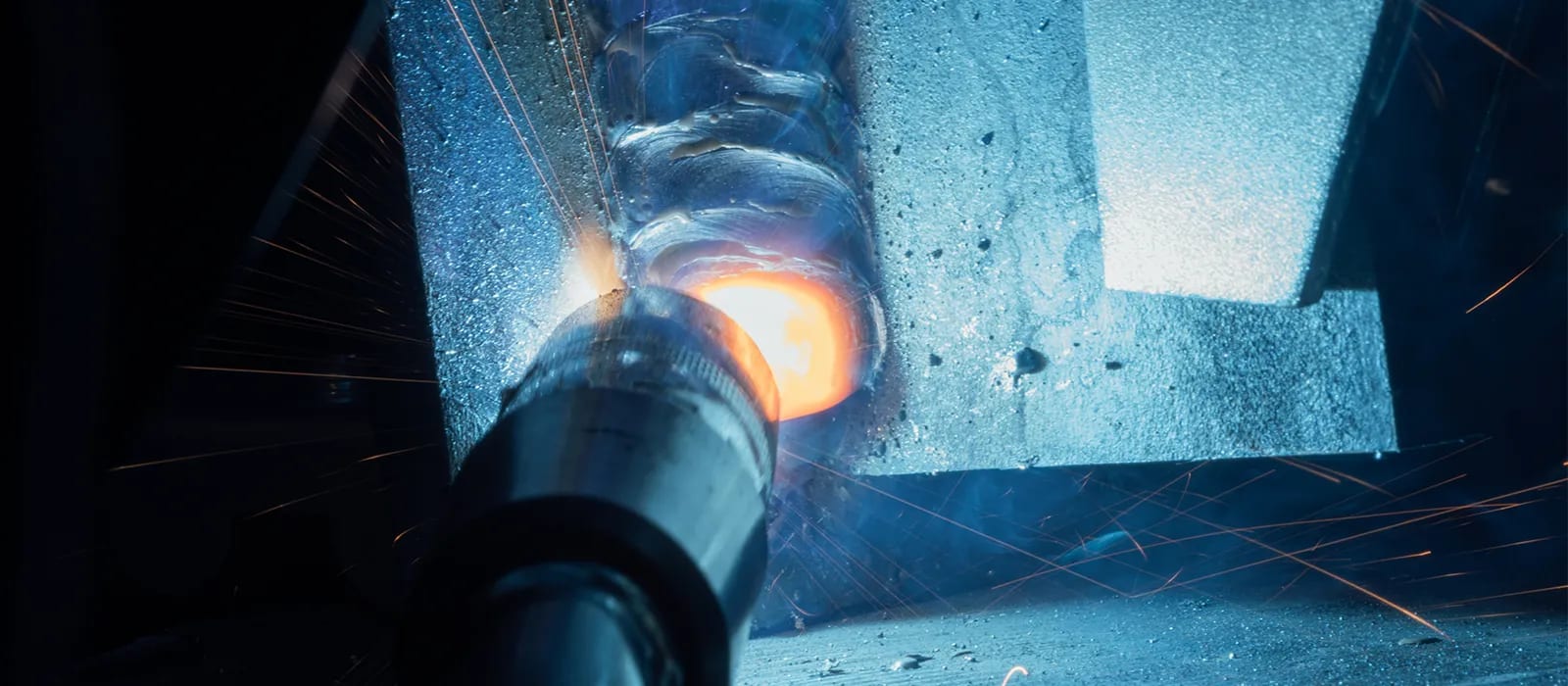
An additional frequent perpetrator behind porosity is the visibility of contaminants on the surface of the base metal, such as oil, grease, or rust. When these impurities are not properly removed prior to welding, they can evaporate and come to be caught in the weld, creating defects. Moreover, using dirty or wet filler materials can introduce contaminations into the weld, adding to porosity problems. To reduce these usual sources of porosity, thorough cleaning of base steels, proper shielding gas selection, and adherence to optimal welding parameters are crucial practices in attaining top quality, porosity-free welds.
Impact of Porosity on Weld Top Quality

The existence of porosity in welding can considerably endanger the architectural honesty and mechanical buildings of bonded joints. Porosity produces spaces within the weld steel, compromising its overall stamina and load-bearing capacity. These voids act as stress and anxiety focus points, making the weld much more susceptible to fracturing and failure under used tons. Furthermore, porosity can reduce the weld's resistance to deterioration and various other environmental elements, additionally diminishing its durability and efficiency.
Among the main repercussions of porosity is a decline in the weld's ductility and durability. Welds with high porosity levels have a tendency to show lower effect strength and reduced capacity to flaw plastically prior to fracturing. This can be especially worrying in applications where the bonded elements are subjected to vibrant or cyclic loading conditions. Porosity can impede the weld's ability to successfully transmit pressures, leading to early weld failure and prospective security hazards in vital frameworks. What is Porosity.
Ideal Practices for Porosity Prevention
To improve the structural integrity and quality of welded joints, what details steps can be executed to reduce the incident of porosity during the welding procedure? Utilizing the appropriate welding technique for the certain material being bonded, such as changing the welding angle and weapon placement, can further stop porosity. Normal evaluation of welds and prompt remediation of any kind of problems determined throughout the welding process are vital methods to avoid porosity and create high-quality welds.
Relevance of Proper Welding Techniques
Executing proper welding strategies is vital in making certain the architectural integrity and top quality of bonded joints, building on the foundation of reliable porosity prevention measures. Welding strategies straight affect the overall toughness and durability of the welded structure. One vital element of correct welding methods is maintaining the proper warmth input. Excessive warmth can result in raised you can check here porosity as a result of the entrapment of gases in the weld pool. Alternatively, not enough warm may result in incomplete blend, producing prospective weak points in the joint. Furthermore, utilizing the suitable welding specifications, such as voltage, present, and travel speed, is essential for accomplishing sound welds with very little porosity.
Moreover, the choice of welding procedure, whether it be MIG, TIG, or stick welding, should align with the certain needs of the task to ensure optimum outcomes. Proper cleaning and preparation of the base metal, as well as selecting the ideal filler material, are also crucial elements of efficient welding strategies. By adhering to these best techniques, welders can lessen the threat of porosity formation and produce top quality, structurally audio welds.

Examining and Quality Assurance Measures
Quality assurance measures play a critical duty in validating the integrity and integrity of bonded joints. Testing procedures are necessary to find and protect against porosity in welding, making sure the strength and toughness of the end product. Non-destructive screening methods such as ultrasonic screening, radiographic testing, and aesthetic assessment are frequently employed to identify possible issues like porosity. These strategies enable the analysis of weld high quality without jeopardizing the stability of the joint. What is Porosity.
Performing pre-weld and post-weld assessments is also critical in keeping quality assurance criteria. Pre-weld inspections include validating the materials, devices setups, and cleanliness of the workspace to prevent contamination. Post-weld evaluations, on the various other hand, evaluate the last weld for any type of problems, including Visit Your URL porosity, and validate that it meets defined requirements. Applying a thorough high quality control strategy that consists of thorough screening procedures and evaluations is paramount to minimizing porosity issues and making certain the total top quality of welded joints.
Verdict
To conclude, porosity in welding can be a typical problem that impacts the high quality of welds. By recognizing the typical sources of porosity and implementing ideal practices for prevention, such as correct welding strategies and testing procedures, welders can make certain top quality and trusted welds. It is vital to focus on avoidance methods to lessen the incident of porosity and keep the integrity More Bonuses of welded structures.
Report this page